Lone Worker Safety Checklist (Complete Guide with PDF)
Our lone worker safety checklist provides an overview of the steps needed to ensure on-site safety of workers is always upheld, including how Onside can help.
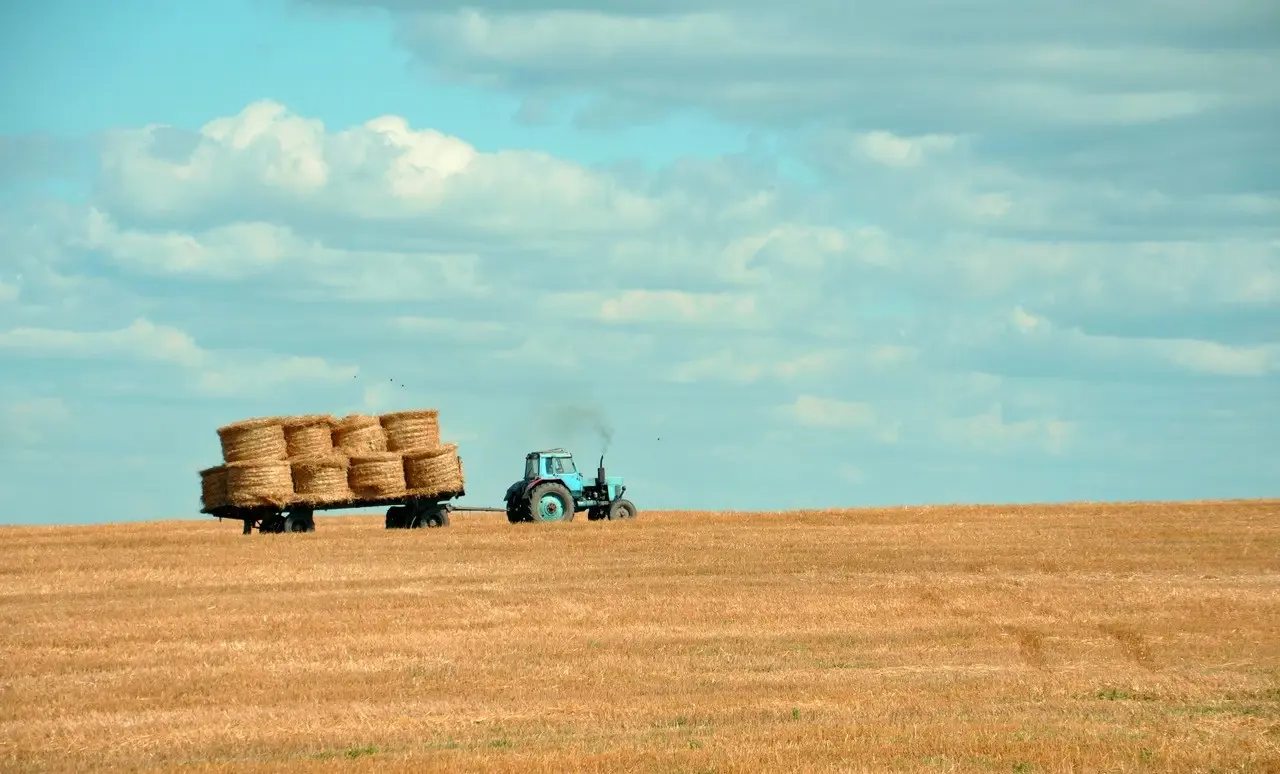
Lone working can pose serious risks for the health and safety of contractors and employees. Most importantly, a medical emergency can become even more dangerous when no one else is on-site to assist. Remote areas also often have limited mobile network access, which compounds the risk.
If lone workers are present on your farm, you need an appropriate safety checklist. This allows you to rest assured that you are taking the necessary steps to protect lone workers on your site.
Download our free PDF lone worker safety checklist template for an easy step-by-step guide to keeping lone workers safe.
What is lone worker safety?
Lone worker safety refers to the steps taken to ensure that remote and isolated workers can safely perform their roles. These steps might include safety and competency training, establishing special lone working protocols, and providing staff with emergency supplies. For a comprehensive solution on your farm, explore our health and safety features.
Due to the common nature of lone working in the rural sector, it is a hugely important consideration on farms and other workplaces. Understanding common farm hazards is also crucial; learn more in our guide to 5 common farm hazards and how to manage them.
Lone workers are workers who conduct tasks in the absence of any other colleagues or supervisors. They might perform tasks with no one else around for part of their day. This might involve travelling to a remote area of a property to fix a fence or perform a similar task.
In locations like cattle stations, workers could be by themselves for weeks at a time. Lone workers in these situations carry out tasks like working with livestock and maintaining fences.
The concept of lone worker safety is enshrined in Australian and New Zealand law. Lone workers are protected under the same workplace health and safety legislation as other employees. On the federal level in Australia, the Work Health and Safety Act (2011) and the Model Work Health and Safety Act (2022) are applicable.
In New Zealand, the most significant parts of workplace health and safety are outlined in the Health and Safety Work Act (2015) and the Health and Safety at Work (General Risk and Workplace Management) Regulations (2016).
As New Zealand is a unitary state, in most cases the national legislation is the only government regulation that applies. However, in Australia, each state and territory also has its own legislation to be followed.
For example, in 2020, Victoria introduced a new criminal offence of workplace manslaughter. This law applies to bodies corporate or other non-employees or volunteers.
If this person breaches their duty under WHS legislation, and a worker dies as a result, they can be charged with this offence.
Consult resources from your local state and territory for more information on lone worker legislation.
Risks associated with lone workers
Under WHS laws, a person conducting business or undertaking (PBCU) must, so far are reasonably practicable:
- Provide and maintain a work environment that is without risk to health and safety.
- Provide adequate and accessible facilities for the welfare of workers.
- Monitor workers’ health and safety and workplace conditions to prevent work-related illness and injury.
- Give workers the necessary information, instruction, training or supervision to do their job without risks to health and safety.
- Consult with workers, and health and safety representatives (HSRs) if you have them, about health and safety issues that may directly affect them.
Regulations of the Model Work Health and Safety Act (2022) specifically address issues associated with lone work. These regulations require PBCUs to:
- Manage the health and safety risks to remote or isolated workers.
- Have systems in place to effectively communicate with workers.
The regulations in New Zealand are broadly similar. These same principles are generally applicable. The New Zealand government gives examples of sensible options to promote the safety of employees working alone, which include:
- A first aid certificate.
- An effective means of getting help quickly in an emergency.
- Regular contact with another person (e.g. another worker).
- If regular contact is impractical, they should check in with another person at regular intervals.
With these guidelines in mind, here are some common risks associated with lone workers in rural settings like farms:
- Electricity and power lines.
- Falls.
- Malfunction of equipment and machinery.
- Accidental start-up of equipment or machinery.
- Animal hazards.
- Acts of violence from other people.
- Social isolation.
- Pesticides and agricultural chemicals.
While many of these risks can apply to any farm, they are made more significant by the fact of lone working. A lack of supervision and oversight makes responding to resulting emergencies far more difficult.
As a result, employing or contracting lone workers adds increased obligations for PBCUs to eliminate or control hazards. Additionally, it is important to have a system in place for responding to them.
Lone worker safety checklist
A lone worker safety checklist enables you to create procedures that ensure the safety of your employees and contractors. It allows you to identify and control the various hazards and risks associated with lone work.
Follow these steps and you will be well on your way to providing a safe workplace for lone workers.
1. Conduct a risk assessment
An important step in any safety checklist is a thorough risk assessment. Unless you are brand new to operating a farm, you should have conducted a risk assessment before.
However, conducting a risk assessment with lone worker safety specifically in mind is an important step. For example, you may never have considered the impacts of social isolation in your risk assessment before.
Some other examples of hazards you might identify include:
- Falls from high places.
- Equipment and machinery malfunctioning or accidentally starting up.
- Animals such as cattle or sheep.
Set aside time to physically travel around your farm and note down any potential hazards. You can simplify this process with Onside's risk reporting functionality. It allows any team member to add risks onto a digital property map.
You can also easily log incidents and near misses digitally, deepening your understanding of risks on your property.
2. Eliminate or control hazards
Having identified potential farm hazards, you must now eliminate or control these hazards wherever possible.
You should have conducted several risk assessments before. As such, you have likely already addressed the "low-hanging fruit" of easily eliminated farm hazards. For example, you may have previously addressed issues like obviously faulty farm equipment.
It is therefore usually necessary to control hazards rather than eliminate them.
One important step in controlling hazards is informing your workers about them. For instance, your lone workers must be aware of areas on your farm where there are dangerous chemicals, such as pesticides, present. You can help ensure everyone on your property knows about hazards with the help of farm safety signs.
Another way to control hazards is to use digital property mapping with tools like Onside. Onside enables you to highlight hazards that might sometimes be obscured, such as electricity lines that are not visible on a cloudy day. Property maps can also be updated by lone workers throughout the day, helping them keep track of any hazards.
3. Equipment maintenance
A critical step for hazard elimination and control on farms is regular and rigorous equipment maintenance. This can greatly reduce the risk posed by farm equipment.
The following steps are a good starting point for your equipment maintenance practices:
- Keep all documents well-organised, including manuals and warranties.
- Maintain a log of each time your equipment is serviced.
- Follow the manufacturer's instructions for regular oil changes.
- Apply lubricants to moving parts of equipment, such as bearings and joints
- Pay special attention to hitches and tires of your equipment.
Onside offers digital farm task management, enabling managers, team members and contractors to handle duties with ease. This feature enables owners to plan, assign, manage and track tasks, ensuring important tasks are carried out properly.
4. Worker medical assessment
Controlling risks posed by your farm is an important part of a lone worker safety checklist. In the case of lone workers, it's also especially important to consider any pre-existing medical conditions they have.
You may employ medically vulnerable individuals who could suffer spontaneous medical emergencies. These individuals will require specific considerations as a lone worker. Examples of such conditions to consider include epilepsy or a heart condition that may result in sporadic cardiac arrest.
Your lone worker medical assessment should be comprehensive. It might include a medical history review and a physical examination. This ensures a holistic approach to controlling risks associated with lone worker safety.
5. Safety and competency training
Safety and competency training is crucial for any rural workplace. It is especially significant for lone workers, as any errors can be many times more dangerous for them.
To ensure your training is effective, it should include significant hands-on elements to it. Distribute regularly updated training manuals, and offer regular refresher courses.
An important principle for workplace health and safety is worker engagement. Workers should be well-versed in WHS practices on your farm.
They should be given time to consider the protocols in place. Finally, they should have an opportunity to share their opinions and contribute to WHS practices.
If the PBCU of a farm does not have personal experience as a lone worker, they may not be aware of important details for lone worker safety. Worker engagement ensures that all perspectives are taken into account to create the best possible outcomes.
6. Establish communication and supervision protocols
Regulations in Australia and New Zealand require PBCUs to establish systems of contact for lone workers.
Onside uses its check-in features to help digitally track lone workers. If workers are not tracked as leaving at the scheduled departure times, Onside will contact them with notifications. Eventually, they will receive a phone call.
Having an emergency response system such as this one in place helps to mitigate the concerns of lone workers. It enables emergency services to be contacted when required, and grants peace of mind for everyone involved.
Communication and supervision protocols are important for mental health, too. You should have systems in place to check in with workers.
These will help to ensure they can effectively cope with the emotional impact of remote and isolated work. This is especially important for workers operating alone for longer periods.
7. Provide emergency supplies
Emergency supplies are especially important when it comes to lone workers. They may become important in situations where medical assistance might be delayed or unavailable.
Emergency supplies you should consider providing to lone workers include:
- First aid kits including bandages, antiseptic wipes, sterline dressings, scissors and tweezers.
- Mobile phones and emergency contact information.
- Torches with spare batteries in case of blackouts, or unexpectedly becoming stranded at night.
- Navigation aids such as a digital map.
- Personal alarm or locater beacon.
8. Provide lone worker safety devices
Lone worker safety devices are tools that are used to monitor lone workers. They can enable supervisors to track isolated workers and quickly identify potential emergencies.
A smartphone is a commonly used lone worker safety device. When paired with software such as Onside, lone workers can access check in features. They can also use a digital map including hazards, and call emergency contacts without needing to memorise the number.
It's an ideal all-in-one lone worker solution.
Other lone worker safety devices include:
- Satellite communication devices. These can offer much of the functionality of a smartphone in areas where mobile coverage is unreliable.
- Wearable buttons which trigger specific events when pressed, such as signalling to an emergency contact.
- Fall detection devices.
- Devices for GPS tracking. This functionality can be built into other lone worker safety devices, such as smartphones or satellite communication devices.
- Safety and operations software such as Onside. Onside includes emergency features available in low connectivity mode, helping to keep staff safe in remote locations.
Decide which lone worker safety device is right for your farm, and distribute them to your lone workers to grant even higher levels of safety.
Keep lone workers safe with Onside
Maintaining lone worker safety can be a major challenge for any rural business. Onside is one tool that can help when putting your lone worker safety checklist in place.
Onside has an automated check-in system for notifying workers and Team Admins when expected check-out times are not met, alerting key contacts. This helps to ensure that lone worker emergencies can be attended to and that persons conducting business or undertaking are maintaining their WHS obligations.
Onside also offers a Team Locator dashboard, simplifying the process of seeing what staff have checked into, and when they expect to leave. These advanced supervision functions make Onside an ideal lone worker safety solution for any farm.
Learn more about using Onside's health and safety features.